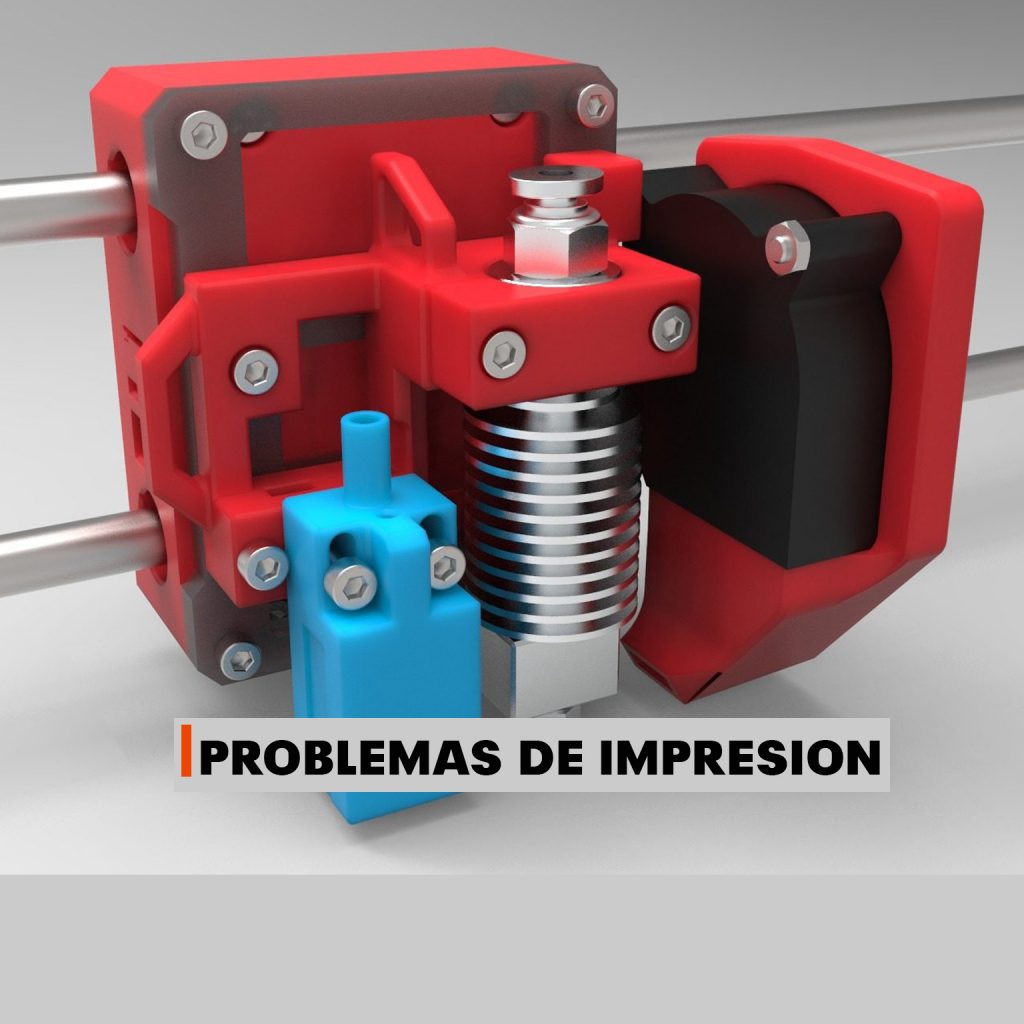
Guía de Problemas de Impresión
– No extruye al iniciar impresión.
“Al comenzar la impresión, no se aprecia plástico en la primera capa” Este problema es muy común que suceda a los nuevos propietarios de impresoras 3D, pero por suerte, también es fácil de resolver. Si la máquina no está extruyendo plástico al comienzo de la impresión, hay cuatro posibles causas. Vamos a tratar cada una de ellas y explicar qué ajustes se pueden utilizar para resolver el problema.
· El extrusor no extruye plástico al comenzar la impresión.
La mayoría de las impresoras, cuando se encuentran preparadas para imprimir (a temperatura de impresión), tienden a rezumar plástico. El plástico caliente en el interior de la boquilla tiende a rezumar de la punta, lo que crea un vacío dentro de la boquilla donde el plástico se haya caliente. Este plástico que rezuma puede ocurrir al comienzo de una impresión cuando se está precalentando la máquina, y también al final de la impresión mientras se está enfriando. Si la impresora ha soltado un poco de plástico debido a esto, la próxima vez que se intente extruir, es probable que tarde unos segundos antes de que el plástico empiece a salir de la boquilla nuevamente.
Si tratamos de iniciar una impresión después de que la boquilla haya rezumado plástico, se puede ver que la extrusión se retrasa. Para resolver este problema, debemos asegurarnos de que el extrusor está lleno de plástico justo antes de comenzar una impresión y listo para la extrusión. Una forma común de hacer esto es mediante la inclusión de algo que se llama una falda . La falda se dibuja un círculo alrededor de la pieza, y en el proceso, se ceba el extrusor de plástico. En Cura, podemos habilitar/modificar este parámetro en el menú de “Expert Settings”, la opción de “Skirt”. Algunos usuarios también pueden preferir para la extrusión de filamento de forma manual de su impresora utilizando los controles de desplazamiento en el panel de control de la máquina antes de comenzar la impresión.
· La boquilla comienza demasiado cerca de la cama.
Si la boquilla está demasiado cerca de la superficie de la base, no habrá suficiente espacio para que el plástico pueda salir del extrusor. El agujero en la parte superior de la tobera se bloquea de modo que no puede salir más plástico. Una manera fácil de reconocer este problema es si la impresión no comienza a extruir plástico para las primeras capas, pero comienza a extruir normalmente alrededor de las capas 3ª o 4ª. La solución será modificar la altura a la que se encuentra la base, recortar la altura del eje Z en la parte de firmware de la impresora o bien regular los tornillos de ajuste de los brazos.
· El filamento no se desplaza por el motor de empuje.
La mayoría de las impresoras 3D utilizan un engranaje pequeño para empujar el filamento hacia atrás y adelante. Los dientes de este engranaje muerden en el filamento y le permiten controlar con precisión la posición del filamento. Sin embargo, si se acumulan virutas de plástico o el diámetro del filamento tiene una variación, parecerá que falta filamento. Si esto sucede, el sistema de engranajes no muerde bien el filamento y no extruye. Por favor, revisa la sección molienda de filamento para obtener instrucciones sobre cómo solucionar este problema.
· El extrusor está obstruido.
Si ninguna de las sugerencias anteriores son capaces de resolver el problema, entonces es probable que el extrusor esté obstruido. Esto puede ocurrir si han quedado residuos dentro de la boquilla, cuando plástico se encuentra caliente dentro de la boquilla demasiado tiempo, o si la disipación del hotend no es suficiente y el filamento comienza a ablandarse fuera de la zona de fusión deseada.
En el caso de utilizar un sistema de guiado de filamento (bowden), lo primero que debemos intentar es retirar el tubo blanco (PTFE) del lado del hotend, y con la máquina caliente intentar retirar el filamento. Una vez lo hayamos hecho, sería conveniente introducir manualmente unos centímetros de filamento y comprobar que extruye correctamente. Si al extruir a mano notamos que hay que hacer mucha fuerza, es probable que tengamos un atasco grave en la boquilla y sería necesario desmontar el hotend.
– La pieza no se adhiere a la cama.
“Durante la impresión de la primera capa, el plástico no se adhiere a la cama” Es muy importante que la primera capa de la impresión está fuertemente adherida a la base de la impresora. Si la primera capa no se está pegado a la base, creará problemas en el futuro. Hay muchas maneras diferentes para hacer frente a estos problemas de adherencia de las primeras capas, así que se examinarán varias causas típicas y se explicará la forma de abordar cada una de ellas.
· La base/cama no está nivelada.
Muchas impresoras incluyen una cama ajustable con varios tornillos que controlan la posición de la cama. Si la impresora dispone de una cama ajustable y hay problemas para conseguir que la primera capa que se adhiera a la cama, lo primero que se tendrá que verificar es que la cama de la impresora es plana y está nivelada. Si la cama no está nivelada, un lado de la cama puede estar demasiado cerca de la boquilla, mientras que el otro lado está demasiado lejos. Lograr una primera capa perfecta requiere una base de impresión nivelada.
· La boquilla empieza demasiado lejos de la cama.
Una vez que la cama está bien nivelada, todavía hay que asegurarse de que la boquilla está comenzando a la altura correcta con respecto a la cama. El objetivo es conseguir que el extrusor quede a una distancia perfecta de la cama (ni demasiado lejos ni demasiado cerca). Para una buena adherencia a la cama, necesitamos que el filamento extruido se pegue ligeramente contra la base. Estos cambios se pueden hacer de forma mecánica, pero existen otras formas de corregir este problema, como son la instalación de un sistema de Autolevel para corrección de camas que no están niveladas, o la utilización de G codes para corregir esa altura incorrecta de la boquilla con respecto a la base (en este caso, será el G-code M206).
· La primera capa está imprimiendo demasiado rápido.
Cuando se extruye la primera capa de plástico, hay que asegurarse de que el plástico se adhiera de forma adecuada a la superficie antes de iniciar la siguiente capa. Si se imprime la primera capa demasiado rápido, el plástico no tiene tiempo para pegarse correctamente a la cama. Por esta razón, normalmente es muy útil imprimir la primera capa a una velocidad más lenta de modo que el plástico tiene tiempo para pegarse bien. En Cura software, este parámetro podemos modificarlo en la pestaña de “Advanced”, sección “Speed” y luego el parámetro “Bottom layer speed”. Una velocidad adecuada se mueve entre los 20 y 50 mm/s.
· Los ajustes de temperatura o de refrigeración.
El plástico tiende a contraerse cuando su temperatura baja drásticamente. Este es un dato importante a tener en cuenta cuando se imprime la primera capa. Si notamos que la primera capa parece pegarse al principio, pero luego se despega nada más se enfría, es posible que los ajustes de temperatura y refrigeración sean los culpables. Muchas impresoras que están destinadas a imprimir materiales de alta temperatura como el ABS disponen de una cama caliente para ayudar a combatir estos problemas. Si la cama se calienta para mantener una temperatura elevada durante toda la impresión, se mantendrá la primera capa caliente de modo que no se contrae.
Así que si la impresora dispone de una cama caliente, es posible tratar de calentar mas la cama para evitar que la primera capa se despegue. Como punto de partida, el PLA tiende a adherirse sin problemas, mientras ABS generalmente funciona mejor si la cama es calefactada. Para mejorar la adherencia de los plásticos a la base, también se utilizan las lacas y otros tipos de adhesivo. Si la impresora dispone de un ventilador de capa, también se puede probar a desactivar el ventilador para las primeras capas de la impresión, para que no se enfríen demasiado rápido.
En Cura software podemos controlar este ventilador desde la pestaña “Advanced” en la sección “Cool”. Se puede ajustar la velocidad del ventilador. Por ejemplo, es posible que la primera capa se haga con el ventilador desactivado y luego encender el ventilador a plena potencia una vez alcanzada una altura determinada. En ese caso, tendremos que añadir dos puntos de ajuste en esa lista: la altura a la que el ventilador comenzará, y el parámetro “Fan speed min” deberá estar al 0%. Si se está usando plástico ABS y hay problemas de adherencia, warping o cracking, es común desactivar o reducir la potencia del ventilador de capa para toda la impresión.
· La superficie de la cama/base (cintas, pegamentos y materiales)
Los diferentes plásticos tienden a adherirse mejor a diferentes materiales. Por esta razón, muchas impresoras incluyen una cama de algún material especial que está optimizado para los plásticos que se van a utilizar en esa máquina. Por ejemplo, varias impresoras utilizan una hoja BuildTak en la parte superior de su cama que tiende a adherirse muy bien al PLA y al ABS. Otros fabricantes optan por una cama de vidrio templado (como vidrio de borosilicato) o espejos, que tienden a funcionar muy bien para el ABS y el PLA cuando se calienta.
Si se va a imprimir directamente sobre estas superficies, asegurarse de que la base está libre de polvo, grasas o aceites antes de iniciar la impresión. La limpieza de la cama con un poco de agua o alcohol puede conllevar a una gran diferencia, sobre todo en la primera capa. El PLA tiende a pegarse bien con laca o con cinta de pintor azul, mientras que el ABS tiende a pegarse mejor con cinta Kapton (también conocida como cinta de poliamida). Muchos usuarios también han tenido éxito usando un pegamento de barra o aerosoles, o usando la combinación de varios
· Cuando todo lo demás falla: Brim y Raft.
A veces, si se imprime una pieza muy pequeña que no tienen suficiente superficie para adherirse a la cama suele salir este problema. Cura software incluye varias opciones que pueden ayudar a aumentar la superficie de contacto y pegarse mejor a la cama. Una de estas opciones se llama “ala” (brim). El ala añade anillos adicionales alrededor del exterior de la pieza, similar a la forma en que el ala de un sombrero aumenta la circunferencia del sombrero.
Esta opción se puede activar en la pestaña de “Basic” en el parámetro “Platform adhesion type” con la opción “Brim”. Cura software también permite a los usuarios añadir una especie de balsa (Raft) bajo la pieza, que también se puede utilizar para proporcionar una base más grande para la adhesión a la cama. Está localizada en el mismo parámetro que el Brim, y dispone de muchos puntos de configuración que se modificarán según la pieza que queramos imprimir.
– Extrusión de plástico escasa.
“Faltan capas, son muy finas, o las capas tienen puntos aleatorios y agujeros en ellas.” Este problema es probablemente el más difícil de encontrar su causa directa ya que hay muchas variables en juego. Cada perfil de impresión incluye la configuración que determina la cantidad de plástico que la impresora 3D debe extruir. Sin embargo, debido a que la impresora 3D no proporciona ninguna información sobre la cantidad de plástico que en realidad sale de la boquilla. Es posible que haya menos plástico saliendo de la boquilla de lo que espera el software (también conocido como under extrusion).
La forma más fiable para probar si la impresora está extruyendo lo suficiente, es imprimir un simple cubo de 20 mm de altura, con al menos 3 perímetros en Cura, “Shell thickness”. Si la boquilla es de 0.4mm, pondremos 1.2mm). Al terminar, en la parte superior del cubo, comprobaremos si los perímetros están fuertemente unidos entre ellos o no. Si hay espacios entre ellos, tenemos falta de extrusión. Si los 3 perímetros se tocan y no tienen ningún hueco, entonces es probable encontrarse con un problema diferente. Si se determina que falta extrusión, hay varias causas posibles para esto:
· Diámetro del filamento incorrecto.
La primera cosa que hay que verificar es que el software sabe el diámetro del filamento que se está utilizando. En Cura software se puede encontrar esta configuración en la pestaña de “Basic” en el apartado de “Filament” (opción “Diameter”). Hay que asegurarse de que este valor coincide con el filamento utilizado. Los valores más comunes para el diámetro del filamento son 1,75 mm y de 2,85. Muchos carretes de plástico también incluyen el diámetro correcto en el envase. También es recomendable medir con calibre varios puntos del filamento para detectar posibles variaciones de diámetro a lo largo del mismo.
· Aumentar el multiplicador de extrusión.
Si el diámetro del filamento es correcto, pero todavía se están viendo problemas de extrusión, entonces será necesario ajustar el multiplicador de extrusión. Se trata de modificar la cantidad de plástico que se extruye (también conocida como flow). A modo de ejemplo, si el multiplicador de extrusión era de 1.0 y se cambia a 1.05, significa que la extrusión de plástico es de un 5% más. Es típico del PLA imprimir con un multiplicador de extrusión de 1 a 0,9, mientras que el ABS tiende a tener multiplicadores de extrusión más cercano a 1,0. Intentaremos entonces aumentar el multiplicador de extrusión en un 5%. Y luego volver a imprimir el cubo de prueba para ver si todavía tiene huecos entre sus perímetros.
Aunque no es lo recomendable, en Cura software podemos incrementar el flujo en el apartado “Flow” de la pastaña “Basic”. Decimos que no es recomendable, porque si la falta de extrusión se produce por un atasco y no porque el multiplicador de pasos del motor de extrusión está desajustado, provocaremos que el atasco empeore.
· Respetar los límites de la impresora.
La causa más simple y probablemente una de las más comunes cuando falta extrusión es simplemente que se está pidiendo a la impresora hacer más de lo que es capaz. La medida de velocidad con que una impresora puede imprimir en el volumen de plástico por segundo es mm3/s. En condiciones ideales una Ultimaker 2 es capaz de imprimir aproximadamente 10 mm3/s. Un límite más realista es de 8 mm3/s. Pero hay que señalar que en este tipo de velocidades la calidad de la impresión no será buena y en función del tamaño del objeto que se va a imprimir podría incluso no soportar tales velocidades debido al tiempo mínimo de enfriamiento de la capa.
Para averiguar qué tan rápido se está tratando de imprimir sólo se tiene que multiplicar el diámetro de la boquilla con la altura de la capa y la velocidad. Así, por ejemplo, si se va a imprimir con boquilla de 0.4mm y 0.2mm de capa a 60 mm/s puede hacer: 0,4 * 0,2 * 60 = 4,8 mm3/s. Esta es una velocidad que una impresora estándar debe ser capaz de manejar sin ningún problema.
· Las temperaturas.
Cuanto más rápido se imprime, menos tiempo tiene el plástico para alcanzar la temperatura de impresión adecuada antes de ser forzado a salir por la boquilla. El plástico a baja temperatura es más denso y requiere presiones más altas para empujarlo a través de la boquilla. Y finalmente, si la presión es demasiado alta provocará la falta de extrusión.
Por lo tanto, ¿se puede aumentar la temperatura para evitar este problema? Sí, se puede, pero dentro de lo razonable. Una temperatura muy elevada puede dilatar el plástico hasta generar un atasco difícil de solventar. Si se tiene que elevar la temperatura más de lo habitual a velocidades normales, es que hay algo más en juego. También es probable que la calidad de impresión se degrade a altas temperaturas, tales como filamento suelto en las paredes o peores voladizos.
· Filamento mordido
Si se experimenta baja extrusión, es habitual encontrarse con que el filamento se ha carcomido en la polea del motor de empuje y es probable que necesite ajustar la fuerza que ejerce la polea sobre el filamento. Tomando como base un extrusor MK8, en la parte superior del motor de empuje, el gatillo dispone de un pequeño tornillo que tendremos que aflojar muy poco a poco (si queda flojo, la polea patinará sobre el filamento y también acabará moliéndolo)
Este tornillo ejerce presión sobre el muelle central y hace que pivote el gatillo sobre su eje, aflojando así la zona de encuentro entre filamento y poleas. Si nos pasamos con la presión sobre el filamento, el motor saltará hacia atrás y no empujará filamento. Cuando el motor de empuje salta hacia atrás, será debido a un atasco o debido a la presión que se ejerce sobre el eje del mismo.
· Filamento enrollado y muy cerrado.
Hacia el final de una bobina de filamento, las vueltas de filamento son generalmente pequeñas y estrechas. Es necesario tener controlada la cantidad de filamento que queda entre la bobina y el extrusor para evitar nudos. Si tenemos sistema bowden, al pasar por el tubo PTFE, el filamento ejercerá más fricción que si estuviera menos enrollado, por lo que es recomendable estirarlo previamente.
· Filamentos enredados.
Esto puede parecer obvio, pero es sencillo asegurarse de que el filamento se puede desenrollar sin problemas. No es raro que una vuelta de filamento se entrecruce en la bobina cuando se retira de la impresora y puede ser difícil de ver. Si la bobinadora de filamento ha fallado, también puede existir algún cruce aleatorio en medio de la bobina.
· Obstrucción de la boquilla/nozzle.
Debido al pequeño orificio de salida en la boquilla no se necesita mucho para que se atasque total o parcialmente. Los atascos pueden tener una amplia variedad de causas tales como contaminantes inesperados en el filamento (con filamento de calidad esto es muy poco probable), exceso de polvo, filamento quemado o residuos de filamentos con un punto de fusión más alto que lo que habitualmente se esta usando.
Aunque se haya cambiado recientemente el material de impresión que requiere temperaturas de extrusión altas (como el ABS) a un plástico con una temperatura de extrusión inferior (como PLA), es importante deshacerse de todo el filamento acumulado en la boquilla. A menudo, puede retirarse el plástico residual de forma manual con el nuevo material a la temperatura requerida para el viejo filamento. Cuando se utiliza una temperatura más alta de lo que se suele utilizar es importante no dejar que el plástico se estanque en la boquilla durante demasiado tiempo. Si lo hace, puede hacer que el plástico se queme y bloquee la boquilla.
Entonces si hay algún bloqueo físico en la boquilla, como la acumulación de polvo o algo por el estilo. Un método sencillo y rápido para empezar es lo que se conoce como el método de “tracción en frío”. Si tenemos un sistema bowden, procederemos a retirar el PTFE del hotend. Calentaremos éste por encima de la temperatura de fusión del último plástico utilizado (subiremos 15-20 grados por encima) y fundiremos manualmente unos cuantos centímetros del filamento nuevo hasta observar que extruye limpio y fluido.
Por lo general, la realización de esta operación unas cuantas veces se hará cargo del problema. Si no es así se puede utilizar un alambre muy fino (o una broca para desatascos) para empujar en la boquilla y ayudar a desalojar lo que sea que está causando la obstrucción. Otra herramienta popular para esto son agujas de acupuntura. Como último recurso, se puede quitar la boquilla por completo y tratar de quemar los residuos en la boquilla con un soplete de propano. Este es un procedimiento bastante tedioso ya que requiere el desmontaje del hotend.
· Combing.
El software de fileteado utiliza un método llamado combing para evitar colisiones y/o hilos sueltos. Cuando el cabezal de impresión tiene que moverse de un punto a otro sin extruir, hace el recorrido de punto a punto por dentro del perímetro de la pieza. Esto hace que cualquier goteo de la boquilla se deposite dentro de la pieza en la que no se ve. En ambos casos, al producirse una retracción del filamento, un efecto secundario puede ser que el depósito en la punta se vacíe muy ligeramente y cuando empieza a imprimir nuevamente, se toma un momento para rellenar el depósito (parámetros también configurables).
Mientras que el depósito no esté lleno, el plástico no será extruido. Cabe señalar que por lo general (y según configuración) esto no es un problema para viajes cortos. Es cuando tiene que hacer un viaje largo que puede causar problemas. En Cura software podemos configurar este parámetro en la sección de “Expert settings” y en el apartado de “Enable combing”. Si no se selecciona “Combing”, se llevará a cabo una retracción y luego se moverá en línea recta cuando se vaya a mover de un punto a otro. Si esta opción no es la que está causando problemas, es posible dejarla desactivada, ya que ahorra un poco de tiempo. Los resultados de esta opción variarán según la geometría de la pieza a imprimir, no hay una elección correcta y definitiva.
– Extrusión excesiva de plástico.
“El plástico de las paredes rebosa y deforma la pieza”
El software está constantemente trabajando en conjunto con la impresora para asegurarse de que la boquilla extruye la cantidad correcta de plástico. Esta extrusión precisa es un factor importante para lograr una buena calidad de impresión. Sin embargo, la mayoría de las impresoras 3D no tienen manera de controlar la cantidad de plástico que realmente se extruye. Si la configuración de extrusión no está correcta, la impresora puede extruir más plástico del que el software espera.
Este exceso de extrusión puede arruinar las impresiones. Para resolver el problema, hay sólo unos pocos ajustes que verificar. Por favor, revisar la sección anterior para una descripción más detallada. Si bien esas instrucciones son para falta de extrusión, se ajustará la misma configuración para el exceso de extrusión, justo en sentido opuesto. Por ejemplo, si al aumentar el multiplicador de extrusión para solventar la falta de extrusión, entonces debería disminuir el multiplicador de extrusión para cuestiones sobre-extrusión.
– Agujeros y huecos en las capas superiores.
“Las caras superiores dejan entrever el interior de las piezas”
Para ahorrar plástico, la mayoría de las piezas impresas en 3D se crean para tener una carcasa sólida que rodea un interior poroso y parcialmente hueco. Por ejemplo, el interior de la pieza puede usar un porcentaje de relleno del 20%, lo que significa que sólo el 20% del interior es de plástico sólido, mientras que el resto es aire. Mientras que el interior de la pieza puede ser parcialmente hueco, queremos que el exterior permanezca sólido.
Para ello, los fileteadores permiten especificar cuántas capas sólidas se desean en la parte superior e inferior de la pieza y en las paredes. Por ejemplo, si está imprimiendo un simple cubo con 5 capas sólidas superiores e inferiores, el software imprimiría 5 capas completamente sólidas en la parte superior e inferior de la impresión. Pero todo lo demás en el medio se imprimiría como una capa parcialmente hueca.
Esta técnica puede ahorrar una enorme cantidad de plástico y tiempo, creando al mismo tiempo piezas resistentes gracias a las distintas formas de relleno de los fileteadores. Sin embargo, dependiendo de la configuración que se esté utilizando, se puede observar que las capas sólidas superiores de la impresión no son completamente sólidas. Es posible que se vean huecos o agujeros entre las extrusiones que forman estas capas sólidas. Si se ha encontrado este problema, aquí hay varios ajustes sencillos que se pueden ajustar para arreglarlo.
· No son suficientes capas sólidas.
La primera opción es para ajustar el número de capas sólidas que se utilizan. Cuando intenta imprimir una capa sólida 100% por encima del relleno parcialmente hueco, el filamento extruido tiende a combarse dentro de los huecos del relleno. Debido a esto, por lo general se imprimen varias capas sólidas en la parte superior de la impresión para asegurar una superficie plana agradable y completamente sólida.
Como habitual, se debe considerar que la sección sólida en la parte superior de la pieza debe ser al menos de 0,5 mm de espesor. Así que si se está utilizando una altura de 0,25 mm de capa, lo que se necesita al menos son 2 capas sólidas superiores. Si se están notando diferencias entre la zona de relleno y la superficie, lo primero que se debe tratar es de subir el número de capas sólidas.
Por ejemplo, si el problema surge utilizando sólo 2 capas sólidas, intentaremos imprimir con 3-5 capas sólidas para ver si el problema se ha solventado. El número de capas sólidas adicionales se producirá dentro de las dimensiones de la pieza y no agregarán tamaño en el exterior del modelo.
En Cura software se pueden ajustar los parámetros de capas sólidas en la pestaña de “Basic” en el apartado de “Fill” con la opción “Bottom/Top thickness”. Este valor tendrá que ser múltiplo de la altura de capa (“Layer height”, tres opciones más arriba) que utilicemos.
· El porcentaje de relleno es demasiado bajo.
El relleno en el interior de la pieza actuará como base para las capas superiores y será el punto de contacto entre las tapas superior e inferior de la pieza. Las capas sólidas tendrán que imprimirse encima del relleno. Si el porcentaje de relleno es muy bajo, habrá grandes espacios vacíos.
Por ejemplo, el uso de un porcentaje de relleno de sólo el 10% (el 90% restante del interior del modelo sería hueco) crearía unos espacios muy grandes que las capas sólidas tendrán que cubrir.
Si se ha intentado aumentar el número de capas sólidas y el resultado todavía no es óptimo, será necesario aumentar el porcentaje de relleno para ver si los problemas desaparecen. Por ejemplo, si el porcentaje de relleno antes era del 10%, se usará un porcentaje del 15-20%. Ya que esto proporcionaría una mejor base para las capas sólidas en la impresión.
· Falta de extrusión.
Si se ha intentado aumentar el porcentaje de relleno y el número de capas sólidas, y sin embargo, se siguen viendo lagunas en la parte superior de la impresión, entonces es probable que haya un problema de falta de extrusión. Esto significa que la boquilla no está extruyendo tanto plástico como el software espera. Para una descripción completa de este problema y cómo corregirlo, por favor leer la sección de “Extrusión de plástico escasa”.
– Hilos o pelos.
“Las piezas dejan pelos de plástico en los cambios de zona de impresión.” Esto es debido a la exudación de plástico de la boquilla mientras el extrusor se mueve. La configuración más común que se utiliza para combatir el exceso de esos pequeños hilos de plástico es algo que se conoce como retracción.
Si está activada la retracción, cuando el hotend se desplaza de una zona a otra de la pieza, el filamento se tira hacia atrás en la boquilla para que actúe como una contramedida contra la secreción. Cuando es el momento de comenzar a imprimir de nuevo, el filamento es empujado de nuevo dentro de la boquilla de manera que el plástico comienza nuevamente la extrusión.
Para asegurarse de que la retracción está habilitada, en Cura software, iremos a la pestaña de “Advanced”, y al segundo apartado, “Retraction”. A continuación, vamos a discutir el valor de retracción, así como otros ajustes que se pueden utilizar para combatir los pelos, como los ajustes de temperatura del extrusor.
· Distancia de retracción.
El ajuste de retracción más importante es la distancia de retracción. Determina la cantidad de plástico que se retrae.
En general, cuanto más plástico se retrae de la boquilla, menos probable es que la boquilla rezume plástico dejando esos hilos.
Los extrusores tipo Bowden pueden requerir una distancia de retracción de hasta 15 mm (en casos extremos, y según características de la máquina). Debido a la distancia entre el engranaje de empuje del extrusor y la boquilla del hotend.
Si vemos hilos en las impresiones, aumentaremos la distancia de retracción 0.5-1 mm y probaremos de nuevo para ver si el resultado mejora.
No es aconsejable superar los 5 mm sin tener conocimientos avanzados de los componentes de la máquina. Uno de los hotend más comunes, el E3D v6, recomienda no realizar retracciones superiores a los 3.5mm para evitar atascos.
· Velocidad de retroceso.
El ajuste que se debe comprobar también en cuanto a retracción, es la velocidad de retracción. Esto determina la rapidez con que el filamento se retira de la boquilla. Si se retrae demasiado despacio, el plástico rezumará lentamente hacia abajo a través de la boquilla y puede empezar a filtrar antes de que el hotend alcance su destino.
Si se retrae demasiado rápido, el filamento puede separarse del plástico caliente dentro de la boquilla (generando un vacío en medio del plástico o incluso llegando a atascar el barrel), o el movimiento rápido puede incluso hacer trabajar en exceso al motor de empuje según las piezas a imprimir.
Por lo general hay un punto en algún lugar entre 20 y 100 mm/s, donde se desempeña mejor la retracción. Un punto de partida ronda entre los 20 y los 50 mm/s para lo que la velocidad de retracción funciona decentemente. Pero el valor ideal puede variar dependiendo del material que se está utilizando y la configuración de la máquina, por lo que será necesario experimentar para ver si con diferentes velocidades disminuyen la cantidad de hilos.
· La temperatura es demasiado alta.
Una vez revisados los ajustes de retracción, la segunda causa más común para los pelos es la excesiva temperatura del hotend. Si la temperatura es demasiado alta, el plástico dentro de la boquilla se volverá muy viscoso y goteará de la boquilla fácilmente.
Sin embargo, si la temperatura es demasiado baja, el plástico todavía será algo sólido y tendrá dificultad para ser expulsado por la boquilla.
Si aparentemente el valor de retracción es correcto, pero todavía se encuentran estos problemas, intentaremos disminuir la temperatura del extrusor de 5 a 10 grados. Esto puede tener un impacto significativo en la calidad de la impresión final.
· Movimientos largos sobre espacios abiertos.
Como ya comentamos anteriormente, los hilos se producen cuando el extrusor se está moviendo entre dos puntos. Y durante ese movimiento, el plástico comienza a rezumar de la boquilla. La longitud de este movimiento puede tener un gran impacto en la cantidad de exudación que se produce. Los movimientos cortos pueden ser lo suficientemente rápidos como para que el plástico no tenga tiempo a rezumar. Sin embargo, los movimientos largos son mucho más propensos a crear pelos. Para evitarlos, deberemos jugar también con la opción de “Combing”.
– Calentamiento excesivo.
Las zonas pequeñas parecen derretidas.” El filamento sale del hotend en una temperatura que normalmente oscila entre los 180 y los 240º C. Mientras que el plástico está aún caliente, es flexible y se puede deformar fácilmente. Sin embargo, cuando se enfría, se vuelve rápidamente sólido y conserva su forma.
La temperatura óptima para cada filamento, es el equilibrio entre la temperatura de fusión y el enfriamiento de manera que puede fluir libremente a través de la boquilla, pero se puede solidificar rápidamente para mantener las dimensiones exactas de la pieza impresa en 3D. Si no se logra este equilibrio, se pueden comenzar a notar algunos problemas de calidad de impresión en los perímetros externos del modelo impreso. El filamento extruido en la parte superior de la pirámide no era capaz de enfriar con rapidez suficiente como para mantener su forma. A continuación veremos varias causas comunes del sobrecalentamiento y la forma de prevenirlo.
· Refrigeración insuficiente.
La causa más común para el sobrecalentamiento es que el plástico no se está enfriando lo suficientemente rápido. Cuando esto sucede, el plástico caliente es libre de cambiar de forma cuando se enfría lentamente. Para muchos plásticos, es mucho mejor enfriar rápidamente las capas para evitar el cambio de forma. Si la impresora incluye un ventilador de capa, trataremos de aumentar la potencia de este para enfriar el plástico más rápido.
En Cura software se puede hacer esto desde la pestaña “Advanced” en la sección de “Cool”. Esta refrigeración adicional ayudará a que el plástico pueda mantener su forma. Si la impresora no incluye un ventilador de capa integrado, es posible estudiar la instalación de un ventilador o el uso de un pequeño ventilador portátil para enfriar las capas más rápido.
· Impresión a temperatura demasiado alta.
Si se está utilizando un ventilador de capa y todavía se ve este problema, es posible que se esté imprimiendo a demasiada temperatura. Si el plástico se extruye a una temperatura más baja será capaz de solidificar más rápidamente y mantener su forma. Bajar la temperatura de impresión 5-10 grados ayudará sustancialmente a solventar el problema. Cuidado de no bajar la temperatura demasiado, ya que de lo contrario el plástico puede quedarse por debajo del punto óptimo de fusión para la extrusión a través de la pequeña abertura de la boquilla.
· Impresión demasiado rápida.
Si se va a imprimir cada capa muy rápidamente, es posible que el tiempo no sea suficiente para que la capa anterior haya enfriado correctamente antes de depositar la siguiente capa. Esto es particularmente importante para las partes muy pequeñas, donde cada capa sólo requiere unos segundos de impresión. Incluso con un ventilador de capa, es posible que se tenga que reducir la velocidad de impresión para estas pequeñas capas y asegurar así el tiempo suficiente para que la capa se solidifique.
En Cura software, podemos determinar el tiempo mínimo de cada capa, es decir, si una capa tarda 5 segundos en imprimirse, podemos indicarle que hasta pasados los 10 segundos, no empiece con la siguiente capa. En la pestaña de “Advanced”, en la sección de “Cool” modificaremos el valor de “Minimal layer time” para conseguir este objetivo. Otra opción para usuarios mas avanzados, sería utilizar el plugin ya integrado en Cura software llamado “Tweak at Z”, en el que podremos cambiar los parámetros de impresión al alcanzar una determinada altura o capa del modelo a imprimir.
· Cuando todo lo demás falla: Imprimir varias piezas simultáneamente.
Si se han probado los 3 puntos anteriores y todavía hay problemas para lograr una refrigeración óptima, hay una cosa más que se puede probar. Crear una copia de la pieza que se está intentando imprimir o importar un segundo objeto que se puede imprimir al mismo tiempo.
Mediante la impresión de dos objetos a la vez, se proporciona más tiempo de enfriamiento para cada capa. El hotend tendrá que moverse a una ubicación diferente en la cama para imprimir la segunda pieza, lo cual ofrece un breve alivio para la pieza principal.
Esta es una estrategia simple, pero muy eficaz para la solución de problemas de sobrecalentamiento.
– El desplazamiento de capas. “Las piezas salen escalonadas.” La mayoría de las impresoras 3D utilizan un sistema de control ciclo abierto. Que es una forma “elegante” de decir que no tienen ninguna indicación de la ubicación real del hotend. La impresora simplemente intenta mover el cabezal de herramienta a una ubicación específica, y espera que llegue allí.
En la mayoría de los casos, esto funciona bien debido a que los motores paso a paso que conducen la impresora tienen suficiente fuerza, y no hay cargas importantes que puedan desplazar el cabezal de herramienta. Sin embargo, si algo sale mal, la impresora no tendría forma de detectar esto. Por ejemplo, si el cabezal tropieza con un hilo suelto o con un borde de la pieza impresa mientras se estaba imprimiendo, es posible que el hotend se haya desplazado. La máquina no tiene forma de detectar esto, por lo que seguirá imprimiendo como si nada hubiera sucedido. Si hay capas desalineadas en la impresión, por lo general es debido a una de las causas siguientes.
· El hotend se está moviendo demasiado rápido.
Si se está imprimiendo a una velocidad muy alta, los motores de la impresora 3D pueden tener dificultades para mantenerse continuamente a esa velocidad.
Si se intenta mover la impresora más rápido de lo que los motores pueden dar, se suele escuchar un sonido de “clack” cuando el motor no logra alcanzar la posición deseada. Al ocurrir esto, el resto de la impresión se desalinea con todo lo que estaba impreso hasta el momento.
Entonces si la impresora se mueve demasiado rápido, trataremos de reducir la velocidad de impresión en un 50% para ver si ayuda. La velocidad de impresión por defecto controla la velocidad general de la impresora (Parámetro “Print Speed”).
También puede ser que la velocidad de impresión sea la adecuada y simplemente se trate de una de las velocidades especificadas en la pestaña de “Advanced” en la sección de “Speed” (habitualmente la velocidad de relleno es más elevada que la de los perímetros, por ejemplo). Si cualquiera de esas velocidades es demasiado alta, puede causar este problema.
Si tras este ajuste de la configuración avanzada los problemas persisten, es posible considerar la disminución de la configuración de aceleración en el firmware de la impresora para proporcionar una velocidad más gradual y lenta.
· Problemas mecánicos o eléctricos
Si el desalineado de capas continúa, incluso cuando se haya disminuido la velocidad de impresión, entonces es probable que existan problemas mecánicos o eléctricos con la impresora.
Por ejemplo, la mayoría de las impresoras 3D utilizan correas que permiten a los motores el control de la posición del hotend. Las correas se hacen normalmente de caucho y reforzadas con algún tipo de fibra para proporcionar resistencia adicional.
Con el tiempo, estas correas pueden estirarse, lo que afecta a la tensión de las mismas. Si la tensión cede demasiado, la correa puede patinar en la polea de transmisión, lo que significa que la polea gira, pero la correa no está en movimiento.
Si la correa se instaló inicialmente demasiado apretada, también puede causar problemas. Una correa demasiado apretada puede crear un exceso de tensión en los ejes que evitará que los motores giren.
Si se comienzan a notar problemas de capas mal alineadas, se debe verificar que las correas de todos los motores tienen la tensión apropiada. Y ninguno está demasiado apretado ni demasiado flojo. Las impresoras 3D también incluyen una serie poleas unidas al eje del motor paso a paso que se aprieta utilizando un pequeño tornillo (un tornillo sin cabeza). Si este tornillo se afloja, la polea ya no gira junto con el eje del motor.
Esto significa que el motor puede estar girando, pero la polea y correas no se están moviendo. Cuando esto sucede, el hotend no llega a la posición deseada. Así que si el problema persiste, se deben verificar todos los elementos de fijación de las poleas de motor.
Hay también varios otros problemas eléctricos comunes que pueden causar que los motores pierden su posición.
Por ejemplo, si no hay suficiente corriente eléctrica en los motores, estos no tendrán la fuerza suficiente para girar.
También es posible que la electrónica del motor pueda recalentarse, lo que hace que los motores dejen de girar temporalmente hasta que la electrónica se enfríe.
– La separación de capas y Splitting.
“Las piezas se agrietan durante la impresión.”
La impresión 3D funciona mediante la construcción del modelo 3D capa a capa. Cada capa sucesiva se imprime en la parte superior de la capa anterior, y al final esto crea la forma 3D deseada. Sin embargo, para que la pieza sea fuerte y fiable, es necesario asegurarse de que cada capa queda correctamente adherida a la capa inferior. Si las capas no se unen bien entre ellas, la pieza final puede agrietarse o separarse. Vamos a examinar varias causas típicas de esto a continuación y proporcionar sugerencias para la resolución de cada una de ellas.
· La altura de capa es demasiado grande.
La mayoría de las boquillas de impresión 3D tienen un diámetro entre 0.3-0.5mm. Estas pequeñas boquillas también crean algunas limitaciones en cuanto a la altura de capa. Como regla general, la altura de capa debe de ser un 20% más pequeña que el diámetro de la boquilla.
Por ejemplo, si se usa una boquilla de 0,4 mm, no se puede ir más allá de una altura de capa de 0,32 mm, o de lo contrario cada capa de plástico no será capaz de adherirse de forma adecuada a la capa inferior. Así que si se detecta que las impresiones se van a agrietar y las capas no están adheridas entre sí. Lo primero que se debe hacer es comprobar la altura de capa en comparación con el tamaño de la boquilla. Intentar reducir la altura de la capa para ver si ayuda a la unión capas.
· La temperatura es demasiado baja.
El plástico caliente siempre se va a adherir de manera mucho mejor que el plástico frío. Si se está seguro de que la altura de la capa no es demasiado elevada, entonces es posible que el filamento necesite una temperatura más alta para crear una unión fuerte.
Por ejemplo, si se trató de imprimir en plástico ABS a 190º C, es probable que las capas de la pieza se separen fácilmente. Esto se debe a que normalmente el ABS necesita ser impreso alrededor 220-240º C para alcanzar su punto de fusión óptimo y crear una fuerte unión entre las capas de la impresión. Así que si este puede ser el problema, se revisará la temperatura correcta para el filamento utilizado.
Se aumentará la temperatura gradualmente para ver si la adherencia mejora. Todos los fabricantes tienen unas temperaturas de extrusión “óptimas”, pero cada máquina es un mundo. Un mismo filamento puede llegar a variar 30-40 grados según la máquina aparentemente. Con esto quiero decir que los termistores no siempre marcan la temperatura correcta, por tanto, no tenemos que ceñirnos a esos rangos del fabricante. Pero si tenerlos como datos orientativos. – Filamento mordido. “El filamento se come en la polea del extrusor y patina.”
La mayoría de las impresoras 3D utilizan un pequeño engranaje de empuje que aprieta el filamento contra otro rodamiento. El engranaje de empuje tiene dientes afilados que le permiten morder el filamento y empujar hacia adelante o hacia atrás. Dependiendo de la dirección de accionamiento. Si el filamento es incapaz de moverse, y el engranaje de accionamiento sigue girando, se puede moler suficiente como para que patine.
Si esto está sucediendo, normalmente se verán un montón de pequeñas virutas de plástico del filamento que se han molido en el engranaje. También se puede observar que el motor está girando, pero el filamento no se está moviendo. También se ha de tener en cuenta que la presión ejercida sobre un filamento puede ser excesiva para otro. Vamos a explicar la manera más fácil de resolver esta cuestión.
· Aumentar la temperatura de extrusión.
Si se presenta este problema, se debe de aumentar la temperatura del extrusor unos cuantos grados, de manera que el flujo de plástico sea más liviano.
El plástico siempre fluirá más fácil a una temperatura más alta, por lo que esta puede ser una opción muy útil y sencilla. Cuidado con no pasarse de temperatura y provocar un atasco en el barrel.
· Impresión demasiado rápida.
Si el problema persiste, incluso después del aumento de temperatura, lo siguiente que se debe hacer es disminuir la velocidad de impresión. Al hacer esto, el motor del extrusor no tendrá que girar tan rápido, ya que el filamento se extruye en un período de tiempo más largo.
La rotación más lenta del motor del extrusor puede ayudar a evitar problemas de molienda. Por ejemplo, si antes estaba imprimiendo a 100 mm/s, pruebe a reducir ese valor en un 50% para ver si la molienda de filamento desaparece.
· Comprobar si hay una obstrucción en la boquilla.
Si se continúa teniendo molienda de filamento después de aumentar la temperatura y ralentizar la velocidad de impresión, entonces es probable que la boquilla está parcialmente obstruida.
Para ello, revisar la siguiente sección de “Extrusor obstruido”.
– Extrusor obstruido.
“Por más que se modifique, la impresora no extruye plástico.”
La impresora 3D debe fundir y extruir muchos kilogramos de plástico durante su vida útil. Para complicar más las cosas, el plástico debe salir del extrusor a través de un pequeño orificio que es tan grande como un grano de arena. Inevitablemente, puede llegar un momento en que algo vaya mal y el extrusor ya no sea capaz de empujar el plástico a través de la boquilla. Estos atascos son por lo general debido a que algo dentro de la boquilla que está bloqueando la salida del plástico. Esto puede ser intimidante la primera vez que sucede, pero vamos a ver varias soluciones que se pueden utilizar para solventar este problema.
· Empujar manualmente el filamento por el hotend.
Una de las primeras cosas que se puede intentar es empujar manualmente el filamento por el hotend. Para ello, seguiremos los pasos vistos anteriormente en la sección de “Extrusión de plástico escasa” en el apartado de “Obstrucion de la boquilla”.
· Recargar el filamento.
Como se comentaba anteriormente, el plástico se dilata al calentarse, por lo que es posible que se haya calentado en el cuerpo del hotend, apretándolo contra las paredes interiores y dificultando su paso o bien se haya encaracolado en una cavidad interna. En este caso, lo siguiente que se debe hacer es retirar el filamento. Con la impresora a la temperatura adecuada, y tras retirar el tubo PTFE del sistema bowden, tiraremos con cuidado del filamento. Una vez que se retira el filamento, usar un par de tijeras para cortar la parte derretida o dañada del filamento. Se carga nuevamente el filamento y comprobaremos si es capaz de extruir con la nueva sección en buen estado del filamento.
· Limpiar la boquilla.
Si no fuera capaz de extruir la nueva sección de plástico a través de la boquilla, entonces es probable que necesite limpiarla. Muchos usuarios han tenido éxito calentando el hotend a 100-150º C y luego tirando manualmente el filamento hacia fuera (con suerte, se traería pegado cualquier residuo que estuviera dentro). Otros prefieren utilizar una aguja/alfiler o una broca específica para empujar el material a través de la punta de la boquilla. Como última opción, se calentaría el hotend y se desmontaría la boquilla para su revisión.
Te gusto?
Nuestra web se mantiene gracias a la colaboración de personas como tú. Si encuentras nuestro contenido útil y quieres ayudarnos a seguir ofreciéndolo, invitamos un Tecito. Al hacerlo, estarás contribuyendo al mantenimiento y mejora de nuestro sitio. ¡Gracias por tu colaboración!